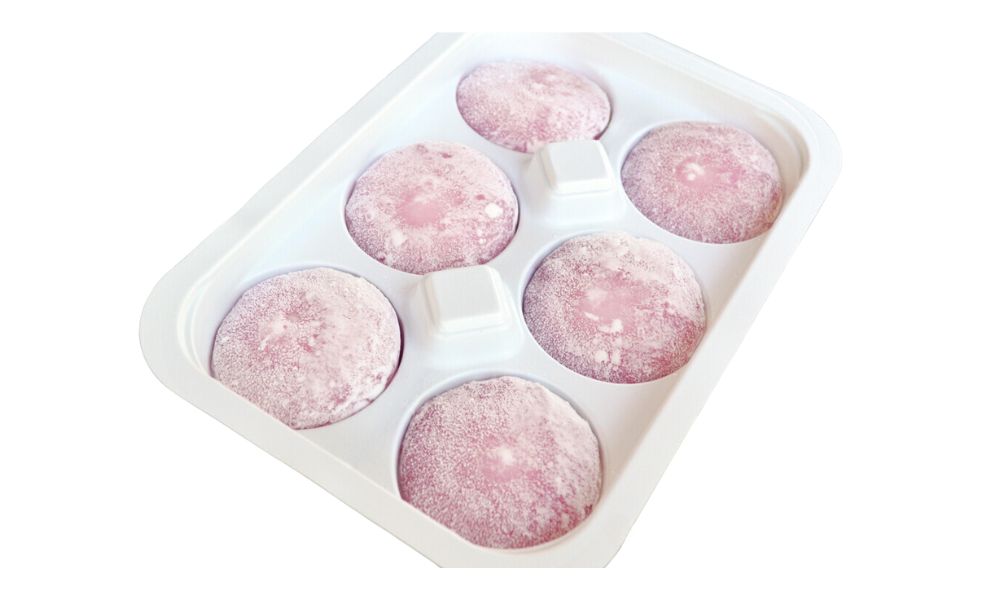
The world of product packaging is continuously evolving, with businesses striving to ensure a perfect blend of functionality, sustainability, and visual appeal. Thermoforming is one such innovative technology that transforms the manufacturing and designs of packaging materials. Continue reading to delve into three primary types of thermoformed packaging designs: plug-assist forming, plug-assist pressure forming, and vacuum forming.
Plug-Assist Forming
Plug-assist forming is a variation of thermoforming that improves the structural integrity and details of the resulting package. This method uses a plug that pushes the softened plastic sheet into the mold cavity. This additional step ensures more uniform wall thickness and improved definition of intricate details.
Benefits of plug-assist forming include:
- • Greater design flexibility with complex shapes and contours
- • More consistent distribution of material thickness
- • Superior detail and definition in the final product
- • Enhancements to strength and durability
Plug-Assist Pressure Forming
Plug-assist pressure forming delivers a high level of precision and efficiency. During this process, positive pressure is added to the mold cavity alongside the plug, which forces the heated plastic sheet into a specific mold design. This technique is ideal for high-quality printed food packaging boxes, providing benefits such as:
- • Crisp, sharp details and graphics
- • Precise material distribution
- • Higher efficiency and consistency compared to conventional methods
- • Greater complexity in design possibilities
Vacuum Forming
The last design type of thermoformed packaging is vacuum forming. This popular thermoforming technique involves heating a plastic sheet until it becomes pliable and then using a vacuum to mold it around a pattern or form. The process is highly versatile and can create thin-walled designs, ensuring optimum flexibility for a wide range of product shapes and sizes.
Some advantages of vacuum forming are:
- • Cost-effective for both small and large production runs
- • Creates lightweight yet durable packaging
- • Short lead times for molds and initial manufacturing
- • Effortless personalization through unique designs
Thermoforming has paved the way for advanced and cost-effective solutions when it comes to product packaging. The three techniques—plug-assist forming, plug-assist pressure forming, and vacuum forming—offer unique benefits to cater to specific packaging requirements. Embrace these innovative packaging designs and watch your products take center stage, enticing customers and driving sales.