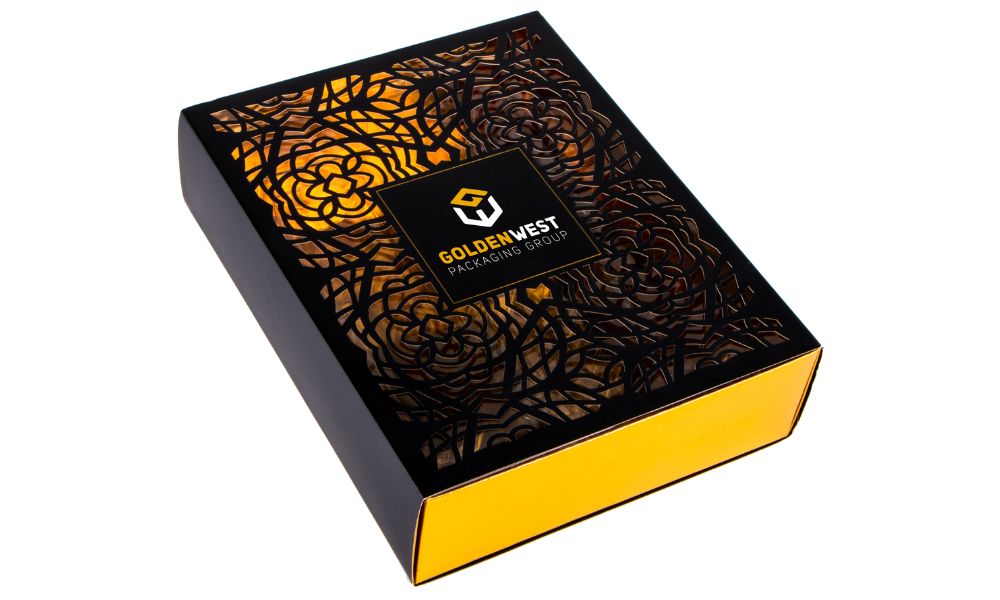
In an industry where precision and versatility are paramount, the die-cutting process in packaging stands out as a testament to innovation and customization. Learn all about the die-cutting process in packaging and explore how this meticulous technique transforms ordinary materials into complex packaging solutions. We’ll dissect the technology and artistry behind die cutting, highlighting its benefits in modern packaging and so much more.
What Is Die Cutting?
Die cutting is a careful process that uses sharp steel blades to precisely cut and mold packaging materials into bespoke shapes. This method allows for intricate designs and structural elements that are essential for both functionality and aesthetic appeal. Die cutting creates packaging that securely encases products while presenting a visually captivating image aligned with the brand.
Die-cutting machinery includes manual, semi-automatic, and fully automatic presses. These machines cater to various production scales and intricacy levels, employing tools like steel rule dies for straightforward designs and rotary dies for high-volume or continuous runs. Each tool is crafted with precision to ensure consistency and accuracy, ultimately delivering cutting-edge packaging solutions.
Benefits of Die Cutting in Packaging
Die cutting revolutionizes packaging with its multifaceted benefits, such as:
- Precision and customization: Dies are engineered with exact specifications for cuts and creases, which means packaging can be tailored to any product’s unique size and shape, enhancing protection and eliminating material wastage.
- Scalability: Whether it’s for a small run of bespoke boxes or mass production, die cutting scales with your products’ demands while maintaining quality and design integrity.
- Speed and efficiency: Die-cutting machines are designed for rapid output, streamlining the production process and reducing turnaround times, which benefits time-sensitive product launches.
- Brand enhancement: With the ability to create complex patterns and intricate details, die cutting facilitates innovative packaging designs that captivate consumers and elevate brand identity.
- Sustainability: By optimizing material usage and enabling the use of eco-friendly materials, die cutting supports sustainable packaging initiatives, which is an aspect increasingly valued by environmentally conscious consumers.
- Cost-effectiveness: Despite the high level of customization it affords, die cutting can be cost-efficient, especially when it comes to large volumes, reducing labor costs and minimizing excess materials.
Die cutting isn’t just a process; it’s a strategic tool for brands to differentiate themselves in a crowded marketplace. To transform your products’ first impressions into lasting impacts, consider harnessing the power of die cutting in your packaging strategy.
Types of Die-Cutting Techniques
Die-cutting techniques vary significantly, each catering to specific needs based on the material, design complexity, and production volume. Here are three primary die-cutting methods utilized in the packaging industry:
Flatbed Die Cutting
Ideal for low to medium production runs, flatbed die cutting uses a hydraulic press and a stationary flatbed where the die board is mounted. The material is pressed against the die, creating precise cuts and creases. This method is known for its cost-effectiveness and is excellent for thicker materials and less intricate designs, ensuring dimensional accuracy.
Rotary Die Cutting
Suited for high-volume projects, rotary die cutting employs cylindrical dies that roll over the material to execute continuous cutting. It stands out for its speed and efficiency, capable of intricate cuts, quick turnovers, and consistent, high-quality outputs. This technique is often chosen for producing large batches of complex packaging designs.
Digital Die Cutting
A modern, innovative approach, digital die cutting forgoes physical dies and instead uses high-precision lasers or blades guided by digital files. This method offers unparalleled flexibility and speed in design alterations and short-run productions. Digital die cutting supports sustainability by minimizing waste and is perfect for prototypes and custom short-run campaigns.
Applications for Die Cutting in Different Industries
Die cutting extends its precision engineering across multiple industries, manifesting in an assortment of applications that underscore its versatility. The pharmaceutical industry, for instance, relies on die cutting for its unrivaled accuracy in producing custom folding cartons that not only prevent tampering but also comply with strict regulatory standards for packaging, keeping medications secure and patients informed.
Within retail, brands utilize die cutting to craft unique promotional displays and personalized packaging, augmenting the consumer unboxing experience and establishing an emotional connection that drives brand loyalty. These varied applications highlight die cutting’s role as an indispensable asset in driving innovation, ensuring quality, and championing sustainability throughout the global market.
The Die-Cutting Process
The die-cutting process involves several critical steps that ensure precision and quality in the final packaging product. Below is a breakdown of these steps:
Design and Engineering
Engineers work alongside designers to create a blueprint that dictates the dimensional specifications, including the product’s shape, size, and function. Attention to detail is paramount here to guarantee that the packaging’s fit and function align with the brand’s vision.
Die Creation
Based on the design, a die is manufactured. This die is a custom-shaped tool with sharp edges that will be used to cut the packaging material.
Material Selection
The choice of material is critical in this process. A business must carefully select the packaging material based on its quality, durability, and sustainability, ensuring it aligns with the brand’s environmental values and the products’ protective needs.
Setup and Configuration
Die-cutting machines are meticulously set up and configured before production begins. This involves securing the die, calibrating the system for pressure and alignment, and testing to ensure accuracy.
Cutting Process
With the setup complete, the die-cutting process begins. The material is fed into the machine and pressed against the die. The pressure applied ensures that the material is cut precisely along the design patterns without compromising material integrity.
Extraction, Trimming, and Quality Assurance
The excess material is removed after the primary cut is complete, and any fine trimming required for intricate designs is conducted. Quality inspections will take place to ensure each unit of packaging meets the standards set in the design phase.
Assembly and Finishing
Some packaging designs require assembly or additional finishing touches, such as folding, gluing, or adding embellishments. This step is vital in providing the ultimate unboxing experience that resonates with consumers. After assembly, the packaging is ready to encapsulate the intended products.
Now that you know all about the die-cutting process in packaging, you’re ready to make informed decisions regarding your packaging strategy. By implementing innovative die-cutting methods, brands can deliver packaging solutions that are not only visually stunning and functionally superior but also aligned with environmental sustainability.
As experts in the field, we are committed to providing services that marry creativity with precision, ensuring that each client’s unique vision is realized in the most efficient way possible. Let’s shape the future of your brand together—contact Golden West Packaging today to explore cutting-edge solutions in packaging innovation!
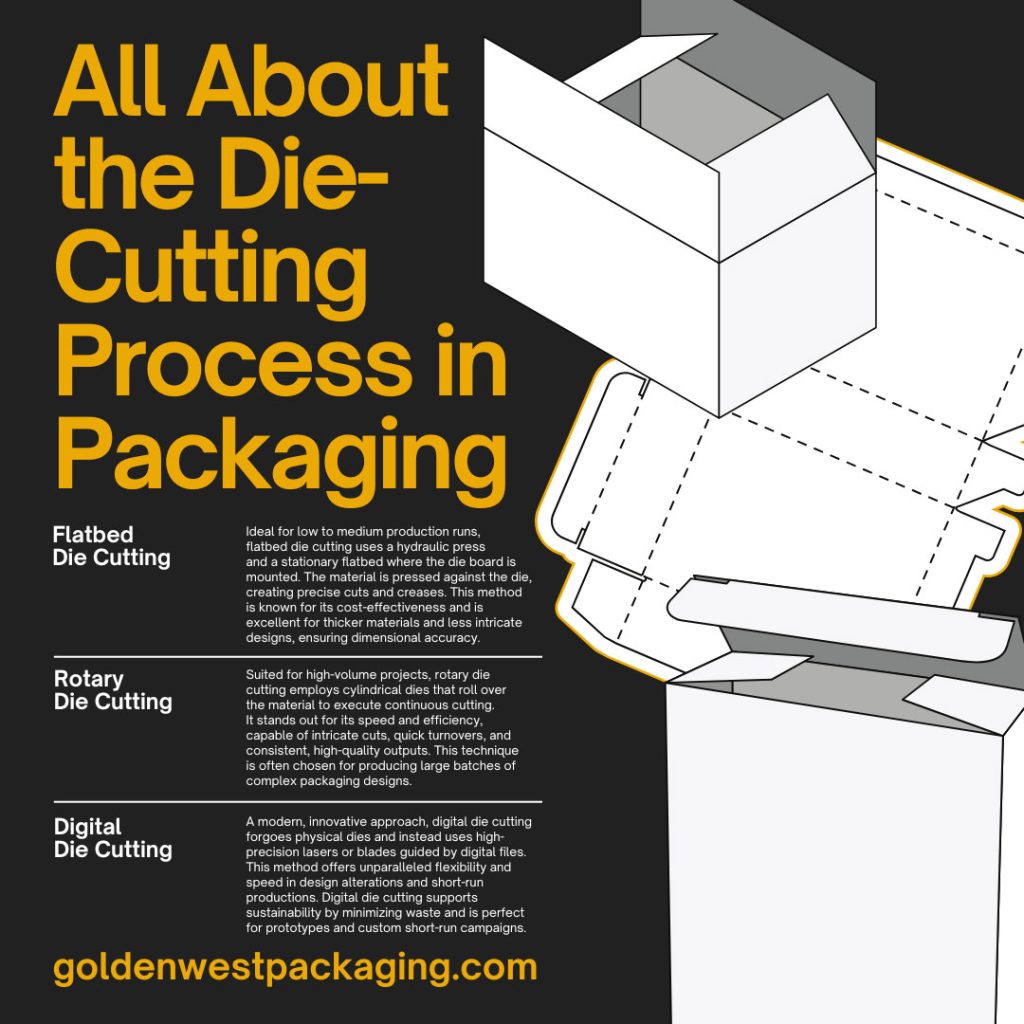